
If you use up all of the engines you received today and the next day's supply of engines doesn't show up, suddenly your assembly line grinds to a halt until the required part is delivered.ĭelivery also impacts production that doesn't use JIT, of course, but the potential for disruption can be significantly reduced by investing in a reserve that you can fall back on if a delivery is late. There's a very obvious problem with just-in-time production though: the reliance on a reliable delivery of materials, which is something that is entirely out of the control of the producer. In the perfect model of this production paradigm, you spend exactly the amount of money you need to in that moment to keep production humming along and not a penny more, which frees you up to spend the money you didn't spend buying excess parts on things like executive bonuses, and stock buybacks that make investors very happy. Heck, why even bother with a warehouse at all at this point if parts can almost literally roll out the back of a truck into the assembly line itself? This way, before you even have time to put an engine on a shelf in your warehouse, you need to put it into the next car that's already rolling down the assembly line.

Refine it even more and you can be ordering 23 engines for the cars you expect to assemble every week throughout the year, or if you wanted to be really efficient, just order deliveries of about three engines a day, every day.

Chip shortage nightmare could last for years, warns IBM.Semiconductor firms report shortage of workers.Semiconductor shortage reaches a new and unwelcome landmark.In our car example, if you are making 100 cars every month, you'll order 100 engines for January delivery, then another 100 for February delivery, another 100 for March, and so on. Like the name described, just-in-time production produces or delivers a product "just in time" for it to be consumed. This is more or less the way things were done though before the adoption of JIT by manufacturers around the world, from the tiniest parts manufacturers making a hinge used in a Samsung Galaxy Z Fold 3 to the industry goliaths like Apple whose MacBook laptops are all delivered on the thinnest of lead times. That money spent on those 500 engines could have been used elsewhere to better maximize profits. This isn't the most efficient way of organizing your production though, since you might use up 100 engines in January, but you still spent the money upfront to buy the 500 other engines that are just sitting idle in the warehouse. In ye olden days of manufacturing, you might have a lot of raw materials stocked up well in advance to produce a certain number of cars, so if you wanted to build 1,200 cars a year, you might order 600 engines in January and another 600 in July. The question is: how big do you build that warehouse? All of them will require you to set up a warehouse to hold all of the raw and refined materials you need to build a car, from aluminum panels to panes of window glass to electronics and computer chips.
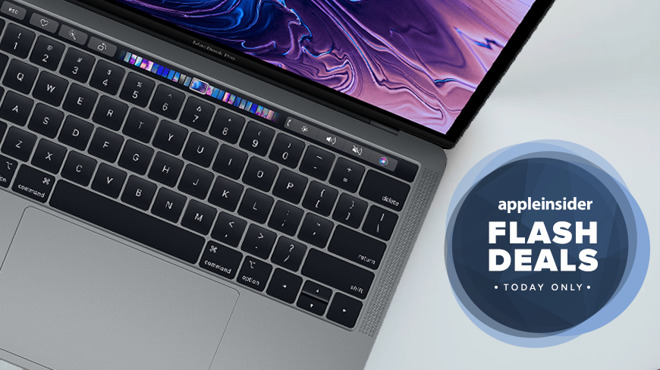

#Sell macbook pro for cash brooklyn mac#
The last-gen Air stays in the lineup, for now, and remains the least expensive Mac laptop for cash-strapped students and schools.If you are going to build a car, for example, there are a couple of ways you can go about setting up your factory. The new Air, however, will start at just $100 less at $1,199 for the base model, and is now the cheapest Apple laptop with a Retina display. The Air was somewhat supplanted by the thinner, lighter 12-inch MacBook model, despite a starting price around $1,299. It is, however, the cheapest Apple laptop starting at $999 and frequently found for less. The old 13-inch MacBook Air, with its processor that's three generations behind and thick bezels around its low-res 1,440x900-pixel display, was last updated in 2017 and hasn't really changed physically since the first model in 2008. These updates were much needed, but they definitely add to the laptop's overall price.
